A printed circuit board (PCB) is the foundation of almost all modern electronic devices. Solder masks play a critical role in ensuring the functionality and longevity of PCBs by covering copper traces, preventing oxidation and protecting against short circuits during the soldering process. There are different types of solder mask available, and each one is tailored to specific applications through its own unique properties. In this article, we look at the six main types of PCB solder masks and highlight their different features, advantages and ideal uses.
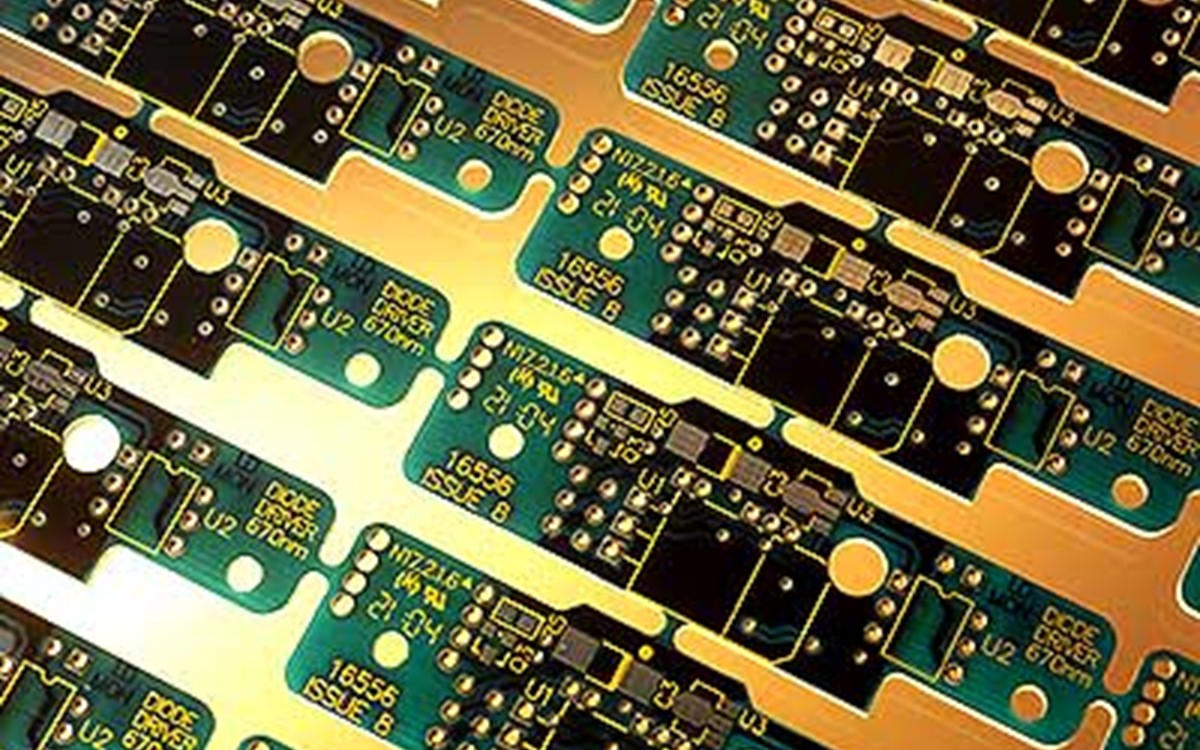
-
Epoxy liquid solder mask
An epoxy liquid solder mask is one of the most cost-effective and commonly used solder masks in the industry. It is made up of a thermosetting polymer that can be applied through screen printing, which makes it suitable for high-volume production processes. These epoxy solder masks have significant insulating properties and the ability to provide strong mechanical protection for PCBs. They are therefore primarily used in applications where things like cost-efficiency are most important and so tend to be found in consumer electronics and mass-produced circuit boards where high precision is not a critical requirement.
-
Liquid photoimageable (LPI) solder mask
A liquid photoimageable (LPI) solder mask can provide excellent precision and is, therefore, one of the most widely used solder masks in modern PCBs. These LPI masks are applied in liquid form and then exposed to ultraviolet light through a photomask, which ensures that only the exposed areas will be cured. This allows for precise patterning and high-definition coverage, which makes LPI solder masks ideal for more complex and dense circuit designs such as multilayer and high-speed circuits. LPI solder masks have been widely adopted in consumer electronics, the automotive industry and telecommunications thanks to their excellent reliability and fine-line capabilities.
-
Dry film solder mask
A dry film solder mask comes in sheet form and is laminated onto a printed circuit board using heat and pressure. It is then exposed to UV light and developed to reveal the desired pattern. These dry film solder masks are best known for their precise thickness control and high chemical resistance. They are often used in high-frequency PCBs and applications requiring this consistent and precise thickness, such as PCBs with fine-pitch components. The popularity of dry film solder masks is due to their accuracy in circuit board manufacturing and are therefore frequently found in boards which are used for the aerospace industry and medical technology.
-
Top-side and bottom-side masks
A top-side or bottom-side mask is specifically applied to either the component side (top) of a PCB or the opposite (bottom). They provide targeted protection for selected PCB areas and can offer enhanced control over soldering processes. The topside and bottom-side solder masks are used when specific regions on the printed circuit board need distinct protection or treatment. This could be during a complex assembly or soldering steps and is commonly seen in double-sided boards and mixed technology assemblies.
-
Ultraviolet (UV) curable solder mask
UV-curable solder masks tend to be unique as they are cured instantly upon exposure to any UV light. They can provide a hard protective coating with high resistance to chemicals and mechanical stress. This offers fast processing times and convenience in manufacturing so UV-curable solder masks are well suited for things like rapid prototyping, small-scale production, and applications where quick curing is necessary. They are often found in manufacturing environments which are focused on high throughput and speed.
-
Peelable solder mask
A peelable solder mask provides temporary protection for specific printed circuit board areas, such as through-hole areas or connectors, during the soldiering process. Once the soldering has been completed, the mask can easily be peeled off, leaving the protected regions unaltered. This means that peelable solder masks can offer excellent resistance to high temperatures and can be removed cleanly without leaving any residue behind. They are ideal when temporary protection is needed during wave soldering, reflow soldering or other processes where certain areas need to be shielded. They are therefore often found in boards with through hole and surface mount components.
These different types of PCB solder masks show how versatile they can be, allowing all industries to take a tailored approach to protecting and enhancing the performance of their electronic circuits. By choosing the right solder mask for the job, manufacturers can ensure optimal functionality, durability, and performance in a wide range of applications. PCB designs are set to continue to evolve and so the adaptability and benefits of solder masks are likely to continue to transform how modern electronics are made and what they might be capable of.
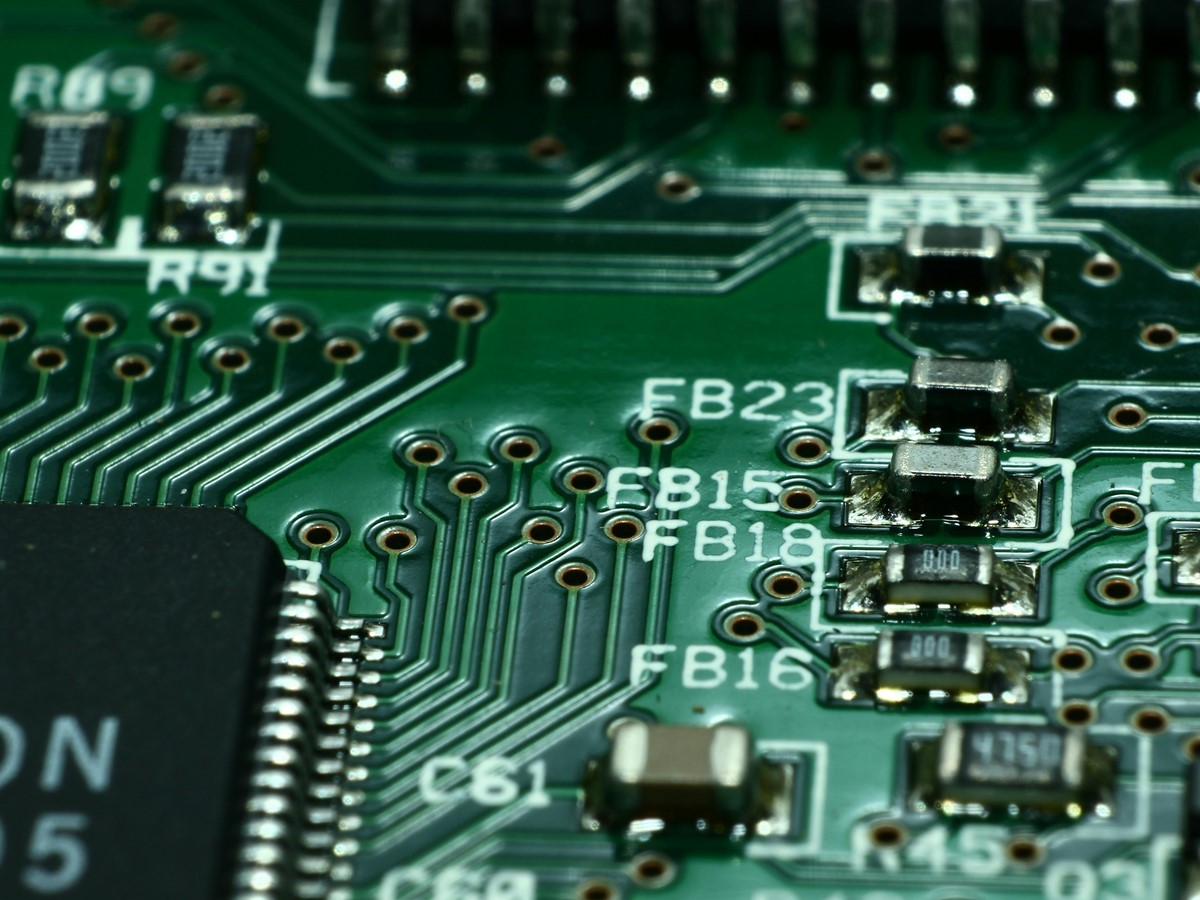