There are many advanced materials and techniques which are relied on by the semiconductor industry to produce high-performance integrated circuits and microelectronic devices. Among these materials, photoresists play a crucial role in photolithography, which is a process used to define and pattern micro-scale features on semiconductor wafers. These photoresists are sensitive to light and enable the transfer of intricate circuit designs onto silicon wafers, therefore creating the basis of most modern electronic components. In this article, we will explore the various types of photoresists that are used in the semiconductor industry and their unique applications.
The properties, mechanism and applications of positive photoresists
A positive photoresist is characterised by its unique response to light exposure. When using positive photoresists, areas are exposed to ultraviolet light and become more soluble in the developer solution. When the resist is exposed to light through a patterned photomask, the exposed regions can be dissolved and therefore leave behind the desired pattern.
Positive photoresists are a huge feature within the semiconductor industry thanks to their high-resolution capabilities. This makes them ideal for creating complex and fine circuit patterns which are most employed in the production of microprocessors, memory chips and other high-density integrated circuits. As positive resists can produce smooth and precise edges, they can ensure that they meet the stringent requirements of modern semiconductor manufacturing, where things like feature sizes continue to shrink.
The use of negative photoresists
As the name suggests, negative photoresists behave in the opposite way to positive resists. This means that when negative photoresists are exposed to UV light, the exposed regions undergo a chemical reaction making them less soluble in the developer solution. As a result, the exposed areas remain intact, and it is the unexposed regions which are washed away during development.
As they work in a different way, negative photoresists are suited to other types of applications. They are best used where robustness and durability are critical and are therefore a common feature in the fabrication of microelectromechanical systems (MEMS), sensors and thicker film applications. As they can produce high aspect ratio features, negative photoresists are also valuable in advanced packaging technologies and specific optical components.
Chemically amplified resist (CARs)
A chemically amplified resist is designed to achieve high sensitivity to light exposure by using a chemical amplification mechanism. An exposure to light will trigger a catalytic reaction that can significantly alter the solubility of the resist material. This allows for faster and more efficient patterning with smaller doses of energy, so CARs are suitable for deep ultraviolet (DUV) and extreme ultraviolet (EUV) lithography.
CARs are increasingly used in the production of next-generation chips and nanoscale devices. As the boundaries of miniaturisation continue to be pushed, CARs can enable high-resolution patterning for devices with features that are measured in nanometres. This is particularly important in the advanced photolithography processes used in state-of-the-art integrated circuits and logic devices.
Dry film photoresists
A dry film photoresist is applied in a solid sheet-like form and laminated onto the substrate using heat and pressure. It offers excellent conformality and uniformity across the surface, making it widely used in printed circuit board (PCB) manufacturing. Dry film resists tend to be used in applications where environmental factors like humidity and temperature must be carefully controlled.
Thick film photoresists
Thick film photoresists have been engineered to create thicker layers, which typically range from tens to hundreds of micrometres. These resists are capable of withstanding high-deposition processes and provide robust structural integrity. They are therefore useful in applications that require elevated structures, such as MEMS, microfluidic devices and certain types of sensors. As they are incredibly durable and have an ability to maintain structural integrity during subsequent processing steps, they are an excellent choice for manufacturing components that need physical depth or height.
UV curable photoresists
A UV-curable photoresist will harden or cure upon exposure to ultraviolet light without the need for any subsequent thermal baking steps. This could help to speed up processing times and simplify several different manufacturing stages. They are frequently used in applications that require these fast-curing times such as optical devices, coatings and micro-patterned components. This makes it easier to achieve increased throughput and reduce production bottlenecks in high-volume manufacturing environments.
Choosing the right photoresist
Any manufacturing process requires you to choose the right photoresist for the job. You therefore need to consider the desired resolution, the thickness of the layer, the substrate material itself and the processing conditions. For example, positive photoresists and CARs are better suited to high-resolution applications due to their ability to produce fine patterns, whilst negative and thick film photoresists are better in applications that require physical durability and elevated structures. For rapid processing, a UV-curable resist can offer the speed and convenience needed for busy production lines.
Photoresists are a crucial part of semiconductor manufacturing as they allow the precise patterning required for modern electronic devices. It is therefore important to understand their different properties and the applications of different photoresist types to allow manufacturers to optimise their processes, achieve higher yields and push the boundaries of technical innovation.
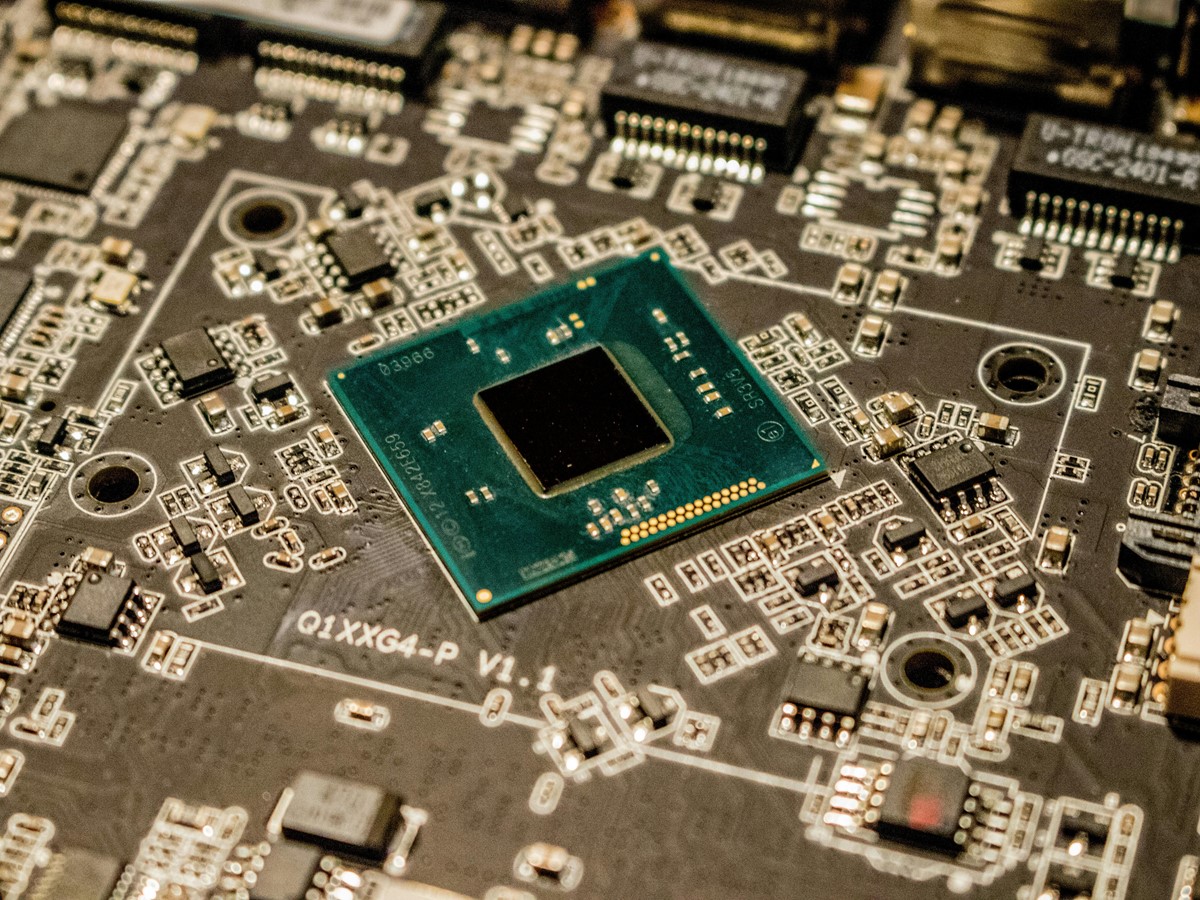
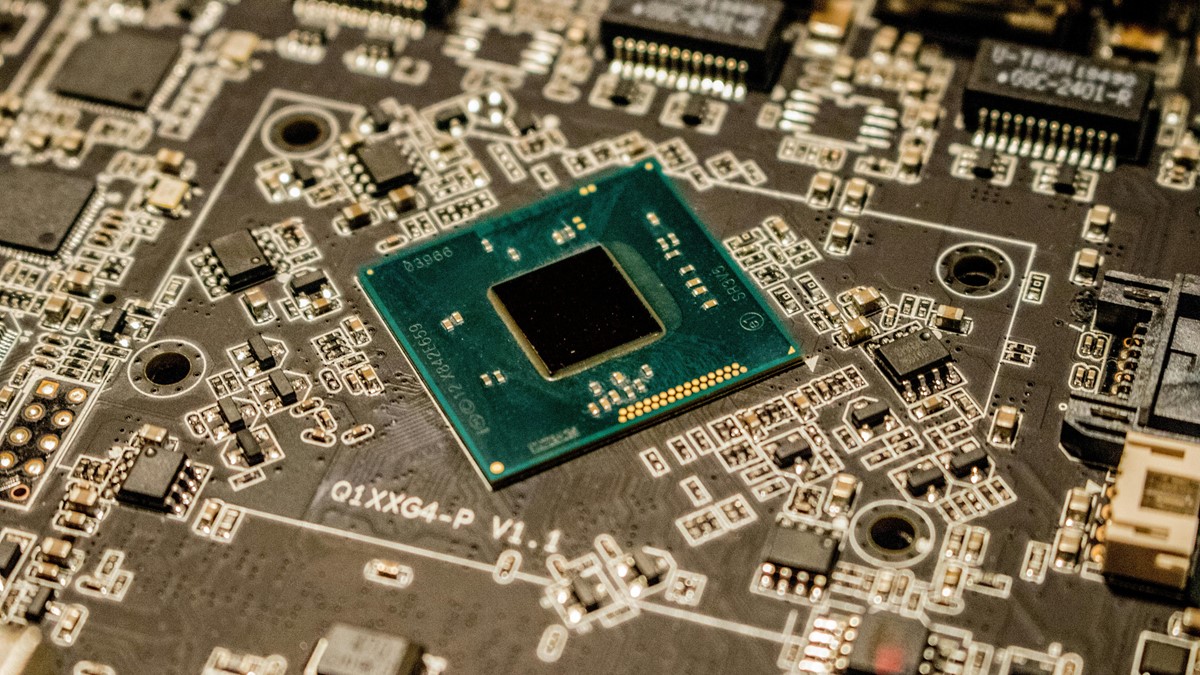