The role of printed circuit boards in modern electronics is to provide the necessary connections and pathways for electrical signals to flow between components. To manufacture these to the highest possible standards, PCB surfaces need to be clean and free from residues that could interfere with their functionality, and this is where neutralisers are essential. These neutralisers are chemical agents which are used to remove any residues that are left behind by the various manufacturing processes, ensuring that PCBs can meet industry standards for both performance and reliability. In this article, we look at the neutralisers that are used in PCB manufacturing and what they do.
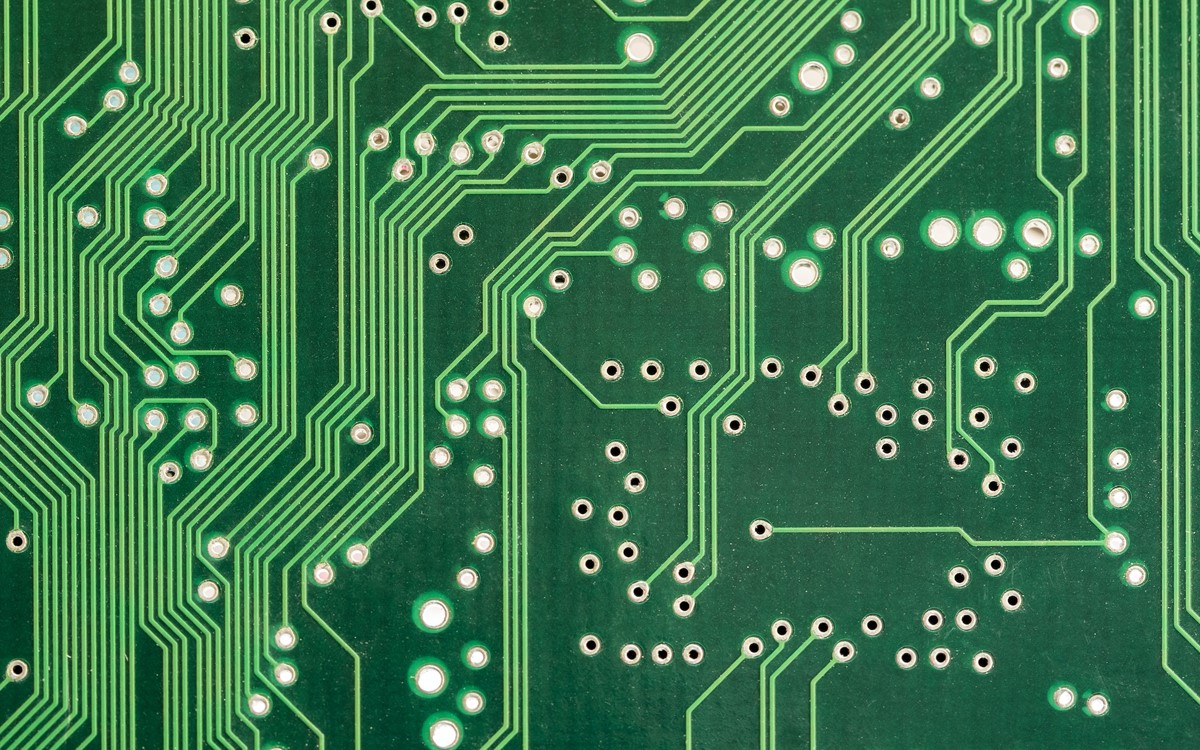
The importance of clean PCB surfaces
A clean surface for a PCB is essential. This is because any contamination that is left on a PCB can lead to things like electrical failures, reduced reliability, and sometimes even a total circuit malfunction. The most common contaminants include flux residues, soldering by-products and chemical remnants from cleaning solutions, which can then cause dendritic growth, corrosion and poor solderability. If this occurs, then the longevity and effectiveness of the PCB can be severely compromised.
It is for this reason that manufacturers implement rigorous cleaning processes to ensure that these contaminants have been fully eliminated. However, they also need to be careful that the cleaning agents themselves do not leave behind any unwanted residues. If the PCB surface has not been properly neutralised, then those residues can lead to several adverse effects such as reduced adhesion of protective coatings, or the formation of conductive paths that can then cause short circuits. This is why neutralisers are a crucial part of PCB manufacturing, as they can prevent such issues occurring by helping to balance pH levels and remove any unwanted chemical traces.
The role of neutralisers in PCB manufacturing
The neutralisers that are used to cleanse a PCB have been specially formulated to counteract and remove all residual acids, alkalis and other contaminants. Typically, they are used as part of the post-cleaning process to ensure that no harmful substances remain.
Removing flux residues
During the soldering process, flux is used to create strong and reliable joints, but its residues, especially from no-clean and rosin-based flux, can leave behind organic acids and ionic contaminants. If these are not properly neutralised, then they can lead to corrosion and electrical failures. Neutralisers are therefore employed to effectively break down residues and ensure that the PCB surface is clean.
Eliminating cleaning agent residues
Often, aqueous and solvent based cleaning solutions are used to remove things like flux and other contaminants and whilst they might be effective, they can also leave behind surfactants, soaps and other residues. As this is likely to impact on the PCB performance, neutralisers are also used to help eliminate these remnants by breaking them down and ensuring that they do not interfere with any subsequent manufacturing steps.
PH balance and corrosion prevention
As part of the cleaning process, there is a risk that a PCB can be exposed to acidic or alkaline environments, which will then alter their surface chemistry. An imbalanced pH will then lead to oxidation which will be consulted joints and reduce conductivity. Therefore, neutralisers are necessary to restore the natural pH of PCB surfaces, preventing any long-term damage and enhancing the durability of the final product.
The types of neutralisers used for PCB cleaning
As neutralisers are likely to be needed for different tasks, there are several different types available. Acidic neutralisers will be used to counter counteract any alkaline residues whilst alkaline neutralisers remove acidic residues, particularly those from fluxes. There are also surfactant-based neutralisers which help to breakdown organic contaminants whilst still maintaining the surface integrity of the PCB. It is important to select the neutraliser based on the manufacturing process and the type of flux or cleaning agent that is being used.
Implementing neutralisation in PCB manufacturing
PCB manufacturers need to work to the highest possible standards, so to ensure optimal results, they need to integrate neutralisation into their PCB cleaning workflows. The initial cleaning stage will remove any major contaminants using solvent or aqueous-based cleaners and then any excess cleaning agents are washed away to prepare for the neutralisation process.
The appropriate neutraliser will be selected and applied to the PCB to remove any lingering residues before a final rinse to ensure that all neutralising agents and contaminants have been completely washed away. The PCB then needs to be thoroughly dried and inspected to verify its cleanliness and ensure that it is ready to move on to the next stage of the manufacturing process.
The benefits of neutralisers in PCB manufacturing
Neutralisers are used in PCB manufacturing to ensure that there are residue-free PCBs to enhance long-term performance and reduce the risk of failures. They also provide better adhesion, as protective coatings and solder masks can adhere more effectively when the surface is clean. Neutralisation can also help to prevent oxidation and corrosion to expand the life of the PCB, and clean PCB surfaces will minimise the risk of short circuits and signal interference.
Residue-free and contaminant-free surfaces are essential in effective PCB manufacturing, as without proper neutralisation there is a risk of electrical failure, corrosion and reduced product reliability. This is why PCB manufacturers now incorporate neutralisers into their cleaning processes to ensure that they are producing high-quality PCBs that are in line with industry standards and capable of delivering optimal levels of performance. With technology continuing to advance at a rapid rate, it is essential that clean PCB surface is a priority, and so neutralisers will continue to be an indispensable component as part of modern PCB manufacturing.
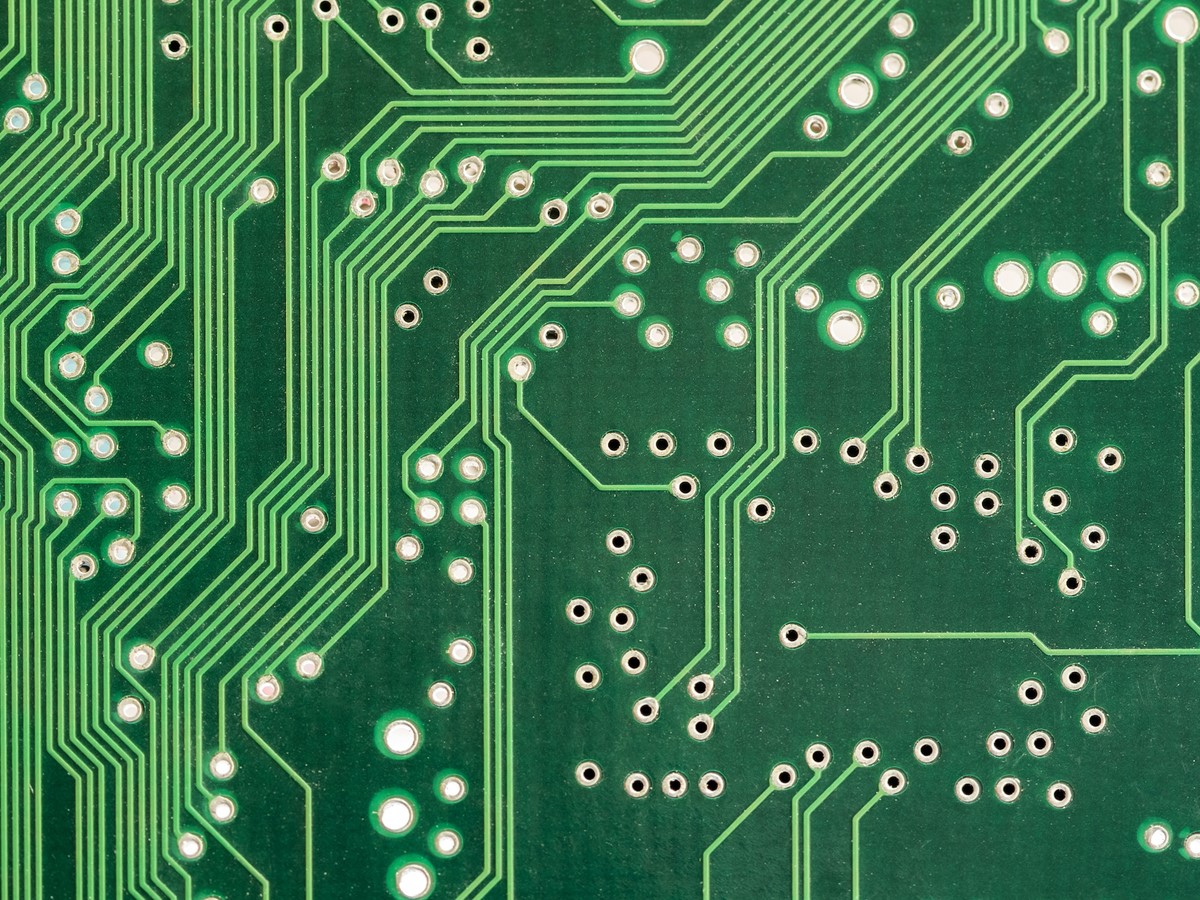