Electrolytic copper coatings are often used in industrial design as they offer exceptional conductivity, durability and corrosion resistance. They have been widely used across a vast number of industries, including electronics, automotive, aerospace and construction, to ensure efficiency and longevity in a variety of applications. It is important for businesses to understand how electrolytic copper enhances industrial performance so that manufacturers can make informed decisions on the best materials and processes for their products. In this article, we look at the role of electrolytic copper, its different applications and how it can help to maximise efficiency in production.
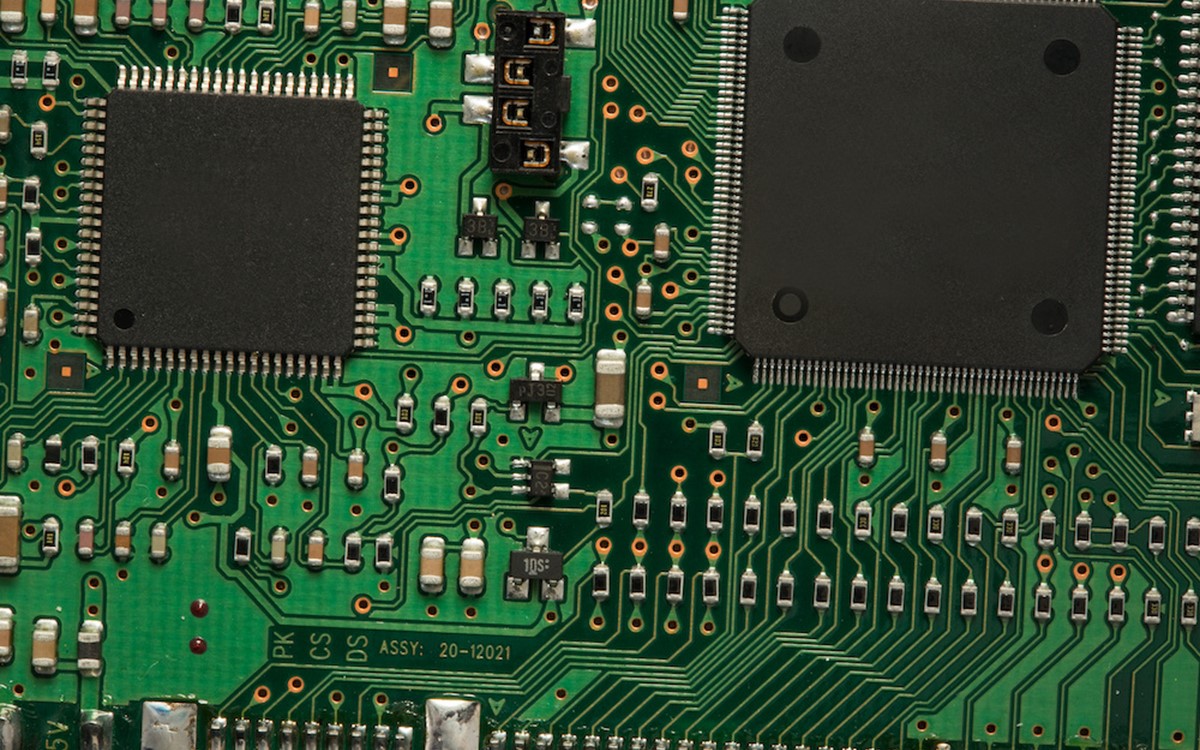
What is electrolytic copper?
Electrolytic copper is a highly refined form of copper that has been produced through electrolysis. This removes impurities, yielding copper that has a purity level of 99.99%. This high purity copper exhibits excellent electrical and thermal conductivity which makes it the perfect choice for coatings in an industrial application.
In electrolytic deposition, a copper anode is dissolved in an electrolytic bath and copper ions are deposited onto a substrate through the application of an electric current. This process is used to ensure of uniform, controlled layer of copper enhancing surface properties of the coated material.
Advantages of electrolytic copper coatings
The main advantage of electrolytic copper coatings is the superior conductivity that they can offer. As copper is second only to silver when it comes to electrical conductivity, it is essential for applications in electronics, power distribution and communication systems. Electrolytic copper coatings have proved extremely useful in reducing energy loss and improving the performance of electrical contacts, circuit boards and wiring components.
Ensuring the longevity of a component can be extremely difficult thanks to issues such as corrosion. Electrolytic copper coatings helped to provide an effective barrier against oxidation and environmental damage, particularly in harsh industrial environments. When these are combined with protective finishes such as nickel or tin plating, copper coatings can extend the lifespan of metal parts exposed to moisture, chemicals and extreme temperatures.
Many industrial applications cause metal components to be subjected to mechanical stress, abrasion and exposure to harsh conditions. Electrical copper coatings are therefore used to help reinforce surfaces, providing additional strength and wear resistance. This has proved to be especially useful to the aerospace and automotive industries, where high performance components are required to withstand continuous use and varying environmental conditions.
Electrolytic copper has also helped to provide an economical solution for many manufacturers without compromising on performance. This is because it is much more cost effective than alternative conductive materials such as silver or gold, making it a preferred choice for mass production in electronics, automotive components and renewable energy applications. Copper coatings have also been found to help reduce material waste by providing thin yet highly efficient conductive layers.
The versatility of electrolytic copper coatings also helps to make them popular, as manufacturers can apply them to various substrates including steel, aluminium and plastic. By using a controlled deposition process it is possible to create a precise coating thickness, making it suitable for applications that require tight tolerances. This is particularly important for printed circuit boards (PCBs), connectors, heat exchangers, and even decorative finishes.
How electrolytic copper coatings maximise efficiency
Electrolytic copper coatings have been found to enhance manufacturing efficiency by enabling faster production processes and reducing waste. Their ability to be applied with precision ensures that there can be uniform coverage, minimising the need for any reworking or additional treatments. This consistency is important in improving product quality as well as ensuring that there are fewer defects and reduced downtime, which can all contribute to significant cost savings and streamlined operations.
The future of electrolytic copper coatings
Electrolytic copper coating technologies are continuing to advance with research and development efforts focusing on enhancing deposition techniques, improving adhesion to various substrates and the development of eco-friendly electroplating solutions. The innovations in nanostructured copper coatings will help to improve conductivity and mechanical strength, making them ideal for advanced electronics and biomedical applications, whilst combining copper with other materials such as graphene or silver to create hybrid coatings can enhance properties like corrosion resistance and electrical performance. The use of sustainable electroplating methods can also help to promote eco-friendly electrolytic processes aimed at reducing chemical waste and energy consumption whilst aligning with global sustainability initiatives.
Manufacturers who are looking for a critical advantage in industrial design are turning to electrolytic copper coatings for their enhanced conductivity, durability and corrosion resistance. The widespread use of these coatings across electronics, automotive, aerospace and renewable energy sectors only show how important they are in the modern manufacturing arena. As industries continue to innovate, electrolytic copper coatings will play an integral role in improving efficiency, reliability, and performance in a variety of applications.
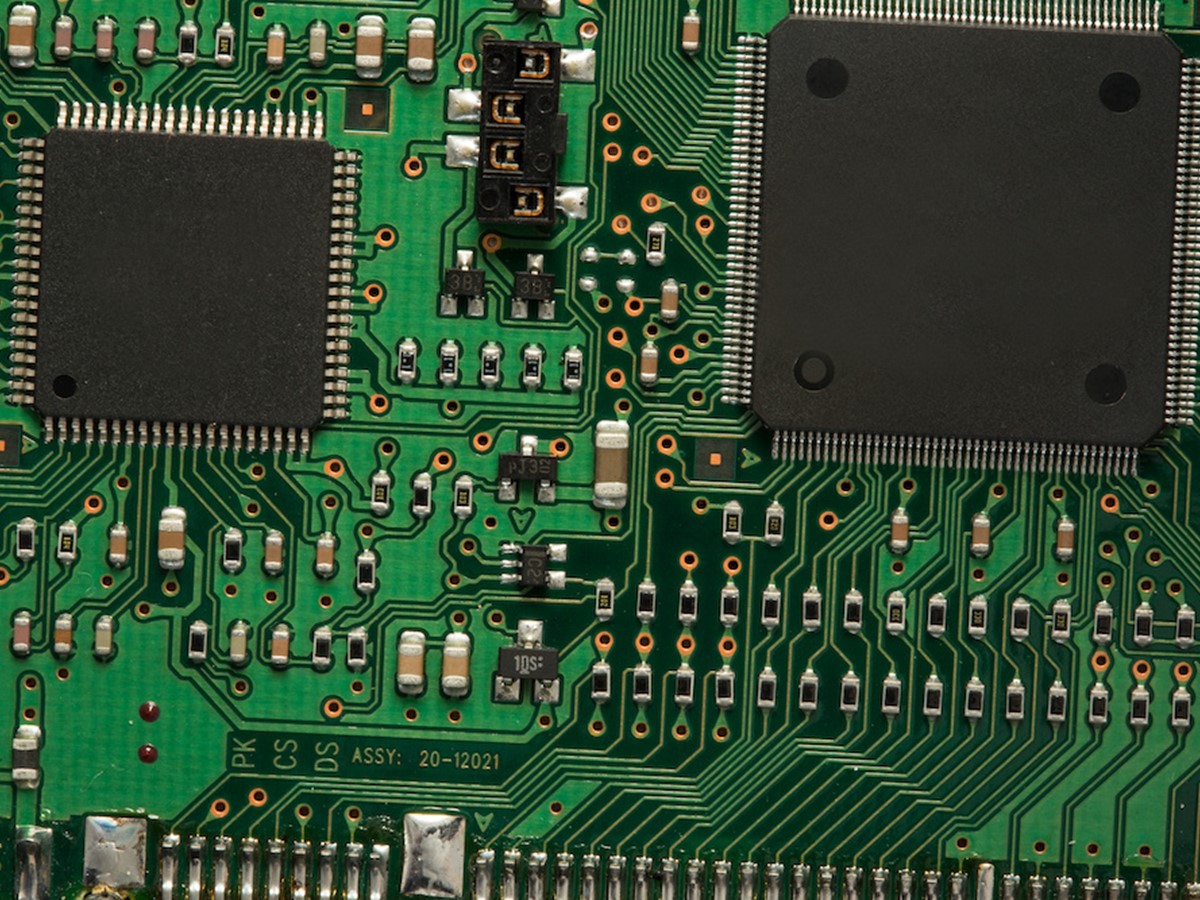