In recent years, semiconductor manufacturing and nanotechnology have taken some huge leaps forward, and this has driven the demand for increasingly precise and complex patterning techniques. As part of this, high-fidelity lithography has become crucial in defining intricate structures with exceptional levels of resolution. Electron beam lithography (EBL) is now a powerful tool to help achieve these goals, with e-beam resists being at the centre of it. These resists are specially formulated materials to enable the creation of advanced patterns with remarkable accuracy, and this is paving the way for the next generation of microelectronics and nanofabrication. Here, we take a detailed look at e-beam resists their role in high-fidelity lithography and what the future holds.
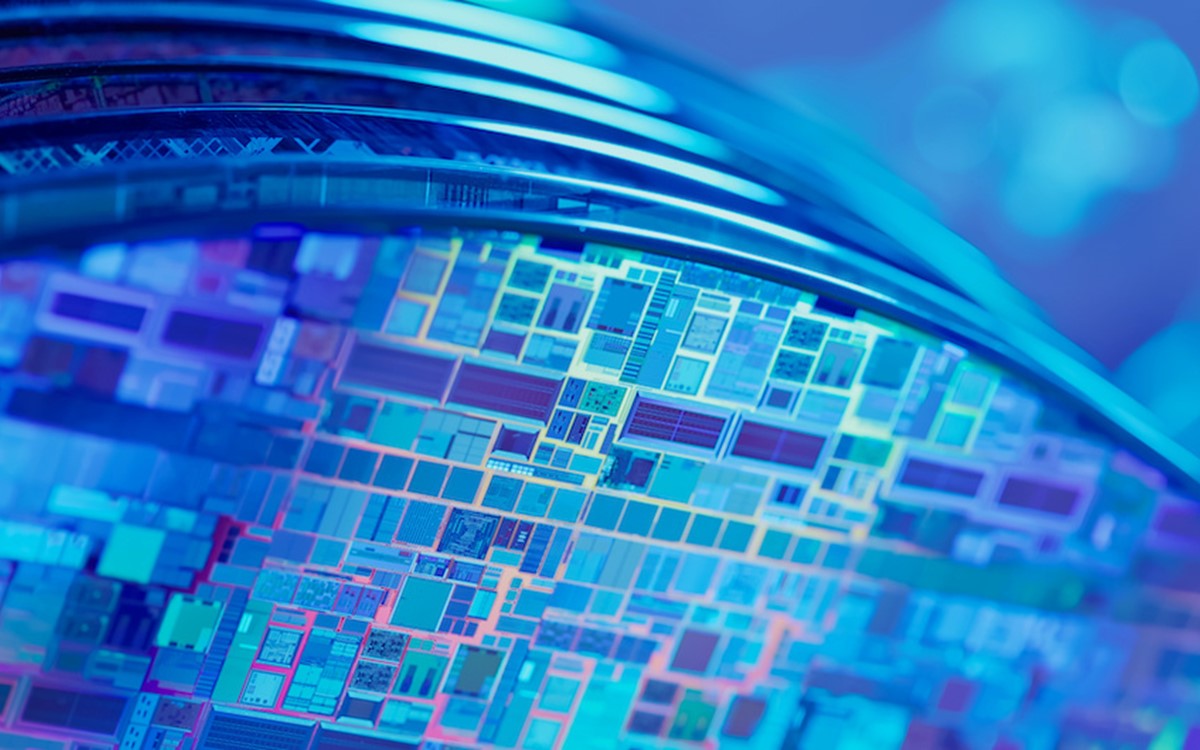
Understanding e-beam resists
An e-beam resist is a polymer-based material that responds to electron beam exposure. This can enable the transfer of high-resolution patterns onto substrates and when subjected to a focused electron beam, the resists will undergo special chemical changes to make them more or less soluble in a developer solution. The e-beam resists are then categorised into either positive or negative resists.
A positive resist will become more soluble in the developer solution after exposure, which then allows the exposed regions to be removed and leaves behind the desired pattern. In contrast, the negative resists will become less soluble upon exposure, and the unexposed areas will be removed, leaving the exposed ones intact. Both types of e-beams are essential to high-fidelity lithography, as they can create sub-10nm features with extreme precision, which makes them an indispensable tool as part of advanced microfabrication.
The role of e-beam resists in high-fidelity lithography
For high-fidelity lithography to be successful, it needs a combination of exceptional accuracy in pattern transfer, minimised distortions and the maintenance of feature integrity. E-beam resists achieve this by offering superior resolution that can define features at the nanometre scale, which exceeds many traditional optical lithography techniques. They also provide enhanced levels of sensitivity, which can allow for faster exposure times and improved throughput in fabrication processes.
In addition to this, e-beam resists provide high contrast between exposed and unexposed regions to ensure the precise pattern delineation and reduced edge roughness that is needed. This all helps to make e-beam resists the perfect choice for any research, prototyping and commercial semiconductor production where precision is the priority.
Advancing lithography with e-beam resists
As modern nanofabrication has become more complex, e-beam resists have had to undergo several significant advancements, including the development of ultra-thin e-beam resists which can define atomic scale features. This is necessary as part of the ongoing drive towards miniaturisation. With modern formulations leveraging novel polymer chemistries to enhance resolution, reduce lineage roughness and improved process stability, e-beam resists can ensure the accurate reproduction of advanced patterns.
E-beam resists have helped to address the limitations of traditional single-layer resists as they are now being developed into multilayer and hybrid resists. These combined different resist layers help to optimise resolution, adhesion and etch resistance, enhancing the fidelity of pattern transfer while maintaining high throughput.
Chemically amplified e-beam resists have been developed to leverage acid-catalysed reactions to enhance sensitivity and resolution. These can allow for reduced exposure doses, improving efficiency in lithographic processes without compromising on pattern fidelity.
There are new possibilities for high-fidelity lithography thanks to the integration of inorganic and hybrid organic-inorganic resists. These offer superior edge resistance, thermal stability, and mechanical robustness which is necessary in advanced semiconductor fabrication.
Applications of E-beam resists in cutting-edge technologies
E-beam resists are now being used in a wide range of high-tech applications such as semiconductor manufacturing, where they enable the fabrication of next-generation transistors, memory devices and integrated circuits. They are also a significant part of photonics and optoelectronics as they help to facilitate the production of nanoscale optical components which are used in advanced communication systems.
Quantum computing is also benefiting from e-beam resists as they can assist in the precise patterning of qubits and superconducting circuits, whilst they have also been found to support the development of lab-on-a-chip devices, biosensors and drug delivery systems in the world of biomedical nanotechnology.
The future outlook for E-beam resists
E-beam resists still face several challenges, such as process complexity, exposure time limitations, and material stability concerns, but with ongoing research addressing these issues at significant rates, it seems likely that novel formulations with improved sensitivity, higher contrast, and enhanced environmental resistance will be with us before we know it.
The future of high-fidelity lithography is reliant on breakthroughs in e-beam resist technology, particularly as semiconductor devices shrink and nanofabrication demands increase. With the continuous innovation that we are already seeing, these materials are set to push the boundaries of what is possible in micro and nanotechnology, which will shape the future of next-generation electronic and photonic devices.
E-beam resists play a part in providing unmatched precision in creating advanced patterns as part of high-fidelity lithography. Their ability to enable nanometre scale resolution, coupled with continuous advancements in material science will ensure their critical role in semiconductor manufacturing, quantum computing and beyond. It seems likely that the next generation e-beam resists will further enhance the capabilities of electron beam lithography, which will solidify their status as a vital tool in modern microfabrication.
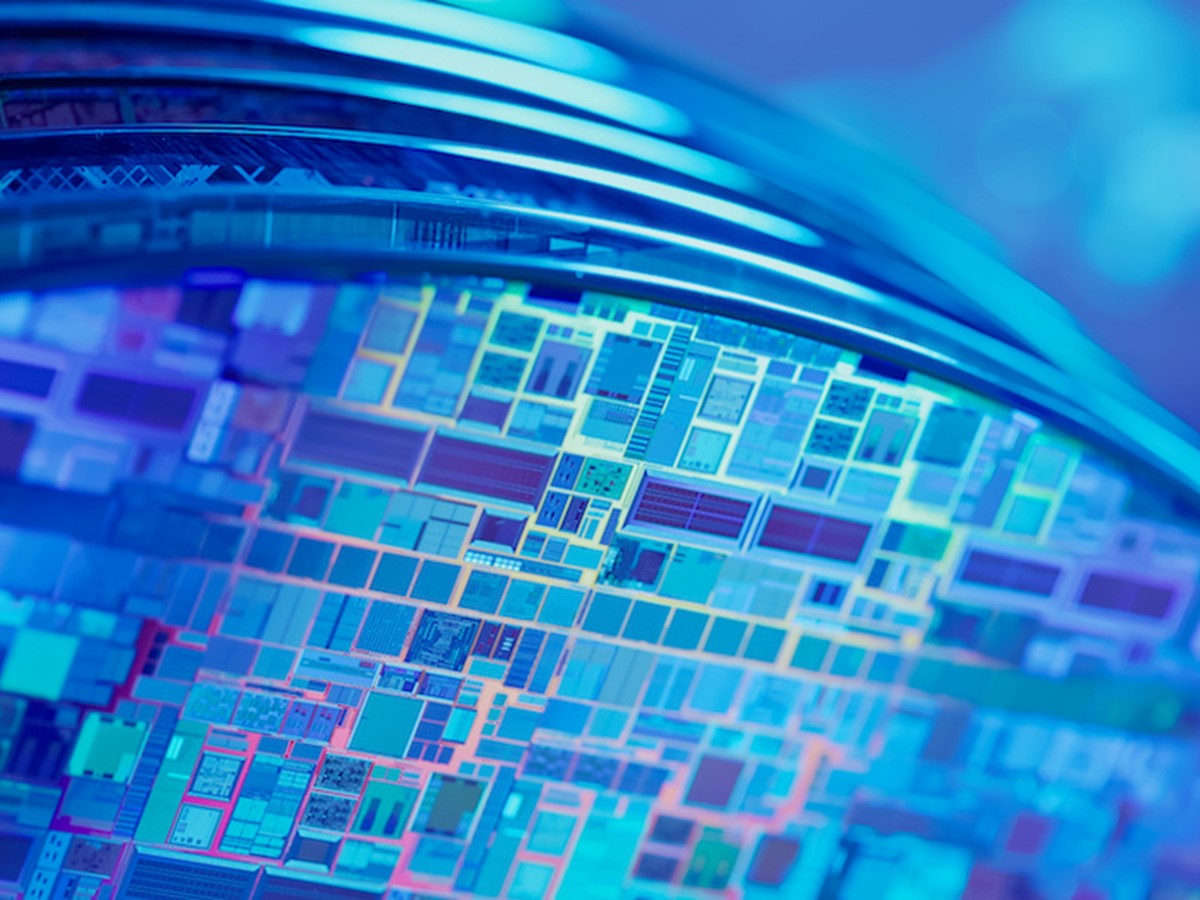