When it comes to semiconductor manufacturing and other microfabrication processes, it is important to make the right choice between using positive and negative photoresists. These are essential in photolithography and play a central role in creating intricate patterns on substrates for electronic components. Each positive and negative photoresist has its own unique properties, advantages and limitations, which means they are suitable for specific applications. In this article, we take a look at some of the key factors to consider when choosing the right type of photoresist for your manufacturing needs.
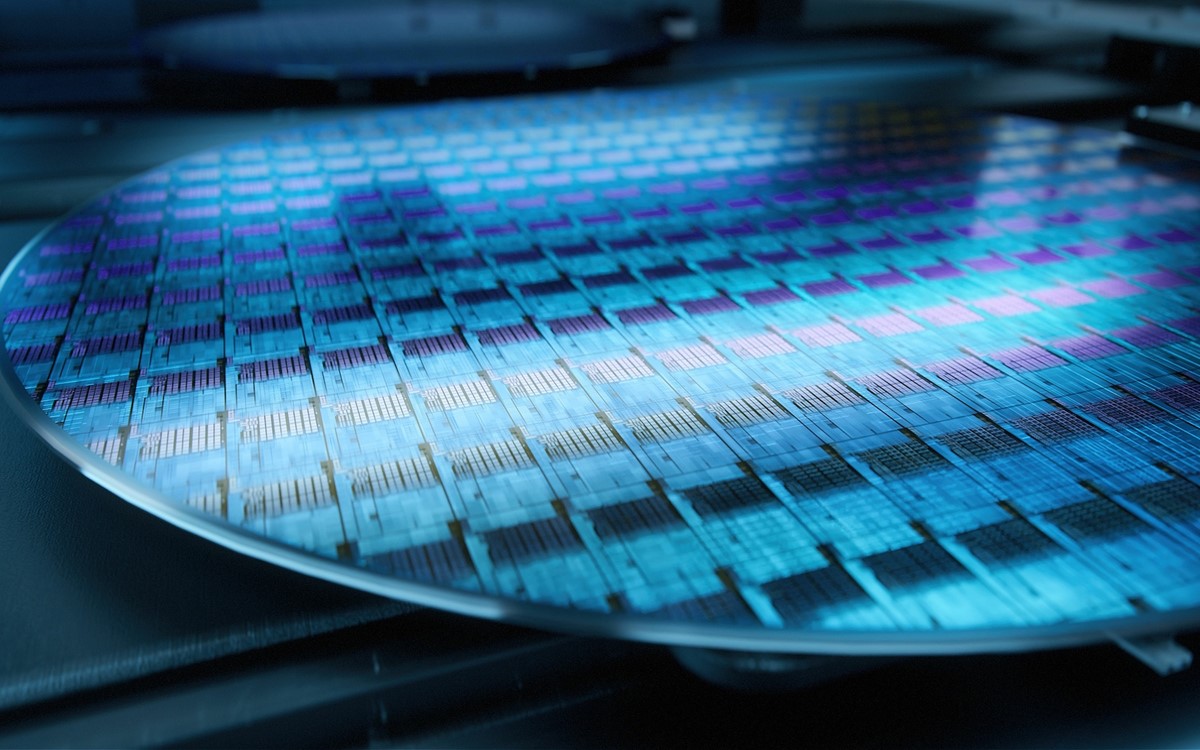
Patterning requirements
When using positive photoresists, the exposed areas become soluble in a developer solution, leaving behind the unexposed areas. The main benefit of this process is that it is able to ensure levels of high precision and sharp pattern edges, which means it is ideal for applications requiring fine detail and high-resolution patterning.
In the case of negative photoresists, the opposite is true, as the exposed areas polymerise and harden, making them insoluble in the developer. They are therefore better suited for applications requiring thicker layers, or where more robust structures are needed.
Generally speaking, high resolution patterns such as those found in advanced integrated circuits or microelectromechanical systems (MEMS) require the use of positive photoresists, however, for larger features or more durable requirements, negative photoresists tend to be the better choice.
Feature size and resolution
As positive photoresists are known for their ability to produce features as small as sub-100 nm, they are better at meeting the stringent demands of modern semi tech conductor technology. Negative photoresists are typically limited to larger feature sizes, however, advances in technology have improved their resolution capabilities. Nonetheless, they are still unable to match the ultra-fine detail that positive photoresists can achieve.
Process complexity and compatibility
A positive photoresist is more compatible with a wide range of wavelengths and exposure methods, whether it is deep ultraviolet (DUV) or electron beam lithography. The downside to this is that their development process can be much more intricate and requires stricter environmental controls. In contrast, negative photoresists have simpler processing steps and shorter exposure times, making them more compatible with traditional photolithography setups such as applications using near-ultraviolet (NUV) light.
Durability and mechanical strength
As negative photoresists form cross-linked polymers upon exposure, they are able to achieve patterns which have excellent mechanical strength and chemical resistance. Their positive counterparts have a lower mechanical strength after processing, so they are less suitable for applications that require robust and long-lasting patterns. This means that negative photoresists tend to be the better option for applications such as electroplating or situations where the resist needs to act as a mask for extended periods.
Etching resistance
Whilst positive photoresists offer moderate resistance to etching, making them suitable for processes requiring controlled material removal, negative photoresists provide a superior etch resistance. This is down to their cross-linked structure which enables them to withstand a much more aggressive etching environment And enables them to maintain pattern integrity throughout harsh etching steps.
Cost and availability
In any form of manufacturing, cost is a very important factor. Positive photoresists often involve much higher material and processing costs due to their advanced capabilities and high resolutions. Negative resists tend to be a more affordable and accessible option, especially for applications where ultra-high resolution is not critical.
Thermal stability
Negative photoresists are known for their ability to excel in thermal stability, meaning they are suitable for processes involving high temperatures, such as thick layer deposition or reflow steps. Positive photoresists can handle moderate heat levels during processing and their thermal stability is less than that of negative photoresists.
Application specific requirements
Each industry and application will have its own unique requirements that will influence the choice of photoresist. Positive photoresists are better suited to advanced semiconductor manufacturing where miniaturisation and precision are critical, whilst negative photoresists are favoured in industries like printed circuit boards (PCB's) and packaging, where larger features and durability are the priority.
Making the choice between positive and negative photoresists will ultimately depend on the specific needs of your own manufacturing process. You will need to consider factors such as resolution, durability, cost, and application requirements to determine the most suitable type. By carefully evaluating these factors, you can then select a photoresist that will ensure the optimal performance, efficiency, and reliability that your project needs.
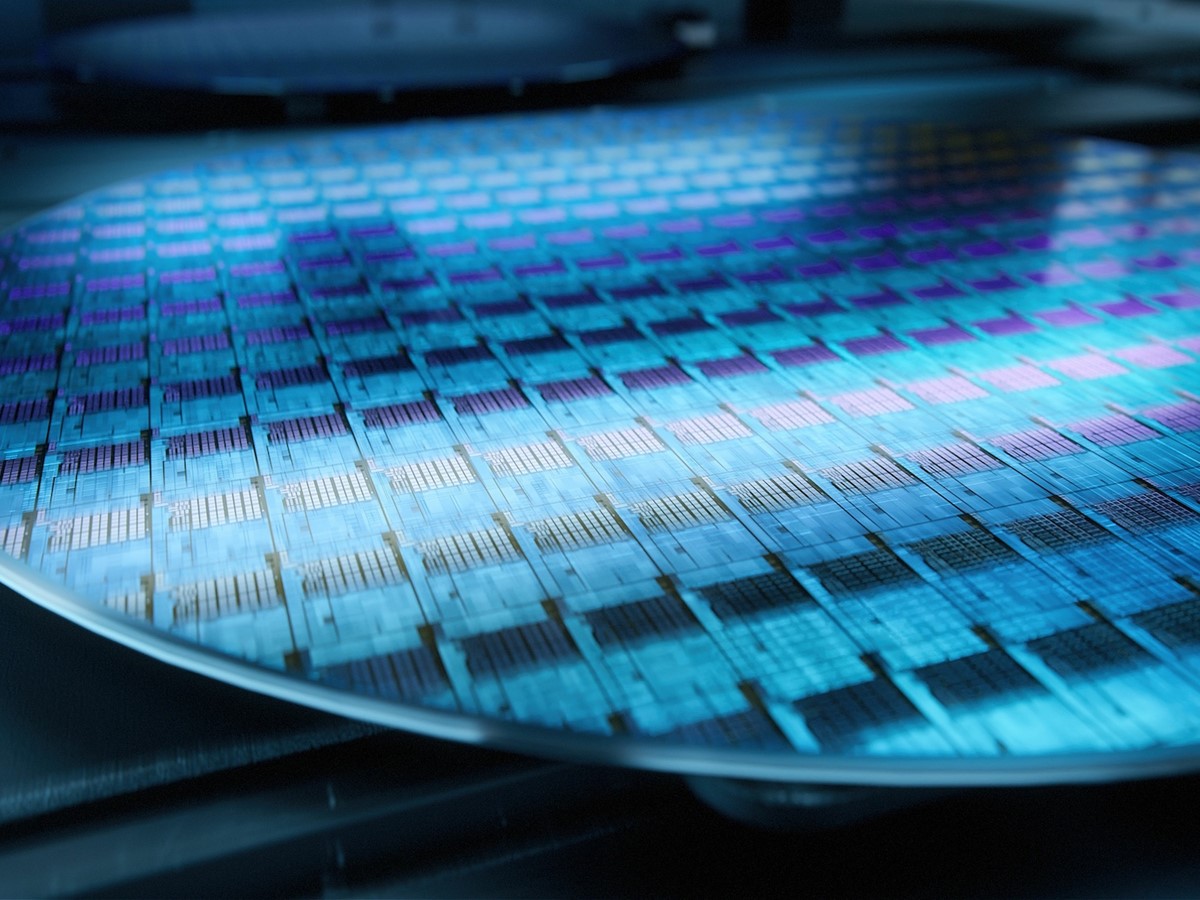